Breaking the Mould:
How recyclers will profit from Thermal Analysis before granulating and compounding
Plastic recycling moves towards higher-quality recyclates and improved material circularity. Partly due to price action, partly due to customer demands and partly due to changing regulations.
Material quality insight is vital to realise the above but one major shortcoming in how material quality is measured, is often overlooked: understanding the material before it enters the extruder. Because, if we can measure earlier in the recycling process, this allows for more process control, reduces costs and, in turn, improves margins by up to 25% per tonne.
Traditionally, most quality control in plastic recycling focuses on post-processing, after the recycling process and granulation, extrusion, or compounding. Yet, by this stage, much of the opportunity for improving product quality and process efficiency has already passed. The real game-changer lies in analysing plastic waste at the flake level, right after sorting (and washing) but before any further processing begins.
The Problem with the Status Quo
Conventionally for pre-processing, analysis tools like NIR (near-infrared) spectroscopy and various handheld (optical) systems are used. However, these often offer limited insight into the true composition of mixed plastic waste, or also require at least 150-200 analyses to calibrate the system and its database. While useful in some cases, these technologies’ main struggles include:
- Dark or black plastics, which absorb (NIR) light instead of reflecting it, making it impossible to identify or qualify.
- Multilayer or composite materials, where often only the top polymer layer is detected or categorised, solely the main fraction is identified or where the material is covered by film layers that block the material beneath.
- Data reliability, these systems require hundreds of reference samples and are prone to user errors.
- Surface-level information, Thermal properties, fillers or processing behaviour are rarely known, whilst crucial for the material processing steps that follow.
Despite our efforts, there are some blind spots in the recycling process that current technologies cannot address. Our industry often still relies on guesswork or indirect indicators to predict how input flakes (and subsequently, the granules) will behave in processing, leading to changing or inconsistent recyclate quality and lost material value. New ways of measuring can help solve some of these challenges.
Introducing MADSCAN®: Thermal Analysis Reimagined
Veridis’ MADSCAN® a technology, uses thermal measurements at a larger, industrial scale and can be applied before extrusion. This is possible because MADSCAN® measures up to 50 grams of material per scan instead of 5 milligrams as conventional technologies (e.g. DSC). Meaning you can measure tens of thousands of flakes accurately at once. This scale allows recyclers to obtain a precise thermal “fingerprint” of their plastic flake mixtures even before melting begins of the extruder begins. Thus, process optimization still can be achieved.

Conventionally, as with DSC, thermal analyses are performed on a ~5mg sample. Effective for virgin or tiny batches, but not providing any applicable information for several tonnes of material.
Here’s what sets MADSCAN® apart:
- Batch-Representative (large) Sample Sizes: Why measure if the results is not representative for what you’re trying to measure?
Traditional DSC analyses ~ 5 milligrams (1 a granule) per scan with one sensor; MADSCAN® scales this up to 50 grams (10.000 flakes or granules) per scan with ~250 sensors, providing statistically meaningful data on real-world waste streams with ~250 separately visible reference points in the sample. - High Accuracy & Subgrade Distinction for Mixed Plastics: MADSCAN® distinguishes not only the main polymer types but also the subgrades of each polymer (e.g., LDPE/LLDPE ratios, PA6, PA66, and PA46 ratios) and quantifies their fractions down to 1%, even for multi-layered materials and black or dark-coloured plastics.
- Pre-Processing Insight, analyse straight from the big bag of flakes/film: Due to MADSCAN®’s sample size, no pre-compounding, extrusion or pre-granulating is needed. Analysis samples for the MADSCAN® T-50 can be pressed from (film) flakes, straight from the big bag, so that you know the exact composition of a batch before processing. With this accurate data, you can directly predict or pre-assess material processing behaviour or even blend compatibility and adjust your plant parameters such as processing temperature accurately per batch.
- Pre-made database & automated analysis: MADSCAN® is developed to be used next-to-the-line. Make & load a sample, hit the button, get the results. Data is processed by the Veridis algorithms and measurement results are uploaded automatically in the digital portal. No need for analysing any graphs yourself.
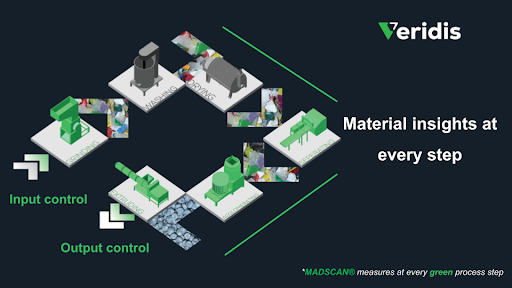
The conclusion
The takeaway for recyclers, converters, and compounders is simple: earlier insight leads to better decisions. By integrating thermal analysis at the flake stage, you unlock three critical advantages:
1. Fewer Surprises
Identify up to X% of thermal outliers before extrusion begins. MADSCAN® detects multi-layer blends, dark materials, and subgrades invisible to optical systems, reducing rework and unexpected line issues.
2. Better Process Control
Tune your parameters to the actual material mix. With per-batch thermal fingerprints, operators can adjust processing temperature, throughput, and blend ratios in advance, improving stability and cutting processing waste by up to Y%.
3. More Confident Batching
Know what’s in your bag. Quantify subgrades and filler fractions down to <Z%, enabling smarter blending decisions and ensuring consistent quality that meets customer specs, especially critical for food-grade or automotive applications.
Thermal insight at the flake stage is no longer optional. It’s becoming the foundation for higher-margin, specification-driven recycling. And it begins long before the first pellet is formed.
Book a meeting with us to discuss your polymer insight questions!
We’d gladly discuss your polymer insights questions and needs to see where MADSCAN® can help your businesses!
We’re currently offering Contract Testing services globally and on-site pilots with the MADSCAN® T-50 in the Netherlands, Germany, Belgium and Northern France. Book a meeting with our team to explore the possibilities!